Carbon nanotubes deliver lightweight de-icing for aircraft
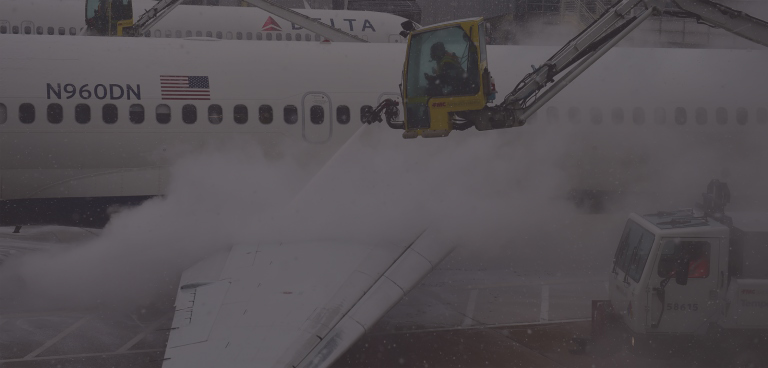
Engineers at Queen’s University Belfast have developed a new lightweight method for de-icing aircraft using a web of carbon nanotubes.
Ice build-up on planes can impact wings, engines and propellers, negatively affecting drag and lift and potentially putting the aircraft in jeopardy. The research, which appears in the journal Carbon, describes how carbon nanotubes (CNT) were used to create a web that was embedded within a glass fibre laminate. When attached to a 4.9 kW m−2 power supply, it was found that that heating performance of the material could remove accreted ice within 15 seconds.
“We started by creating a ‘CNT web’, where individual CNTs are aligned in the draw direction, and horizontally stacking 10-40 layers of the webs, at different orientations, to achieve the desired heating characteristics,” said project lead Professor Brian Falzon, from Queen’s University’s School of Mechanical and Aerospace Engineering. “Each layer of CNT web can be as thin as 1/2000 the thickness of a human hair and the weight of a web large enough to cover a football field would be less than 30 sheets of A4 photocopy paper.
“These CNT webs were cured within a thin glass fibre laminate to provide structural support, and connected to a power supply. When we carried out testing, we discovered that the newly developed CNT heaters achieved rapid heating which shows that (they) could quickly de-ice aircraft and provide effective ice protection in flight.”
Current ice-protection on aircraft usually consist of engine heat rerouted to internal piping within the wings. According to the researchers, the system is inefficient, particularly given the growing use of composites in aircraft construction. What’s more, it adds substantial weight to the wings, further reducing the overall efficiency of flight.
“Compared with state-of-the-art heating systems currently used on aircraft, the CNT heater that we have created at Queen’s is lighter, provides rapid and more uniform heating and is more energy efficient,” said Dr Xudan Yao, a PhD student from China that worked on the project. “It is also more flexible in terms of fitting the shape and performance of any surface or power requirement to achieve rapid anti-icing and de-icing.”