Improved understanding of plasma source for synthesis of carbon nanotubes
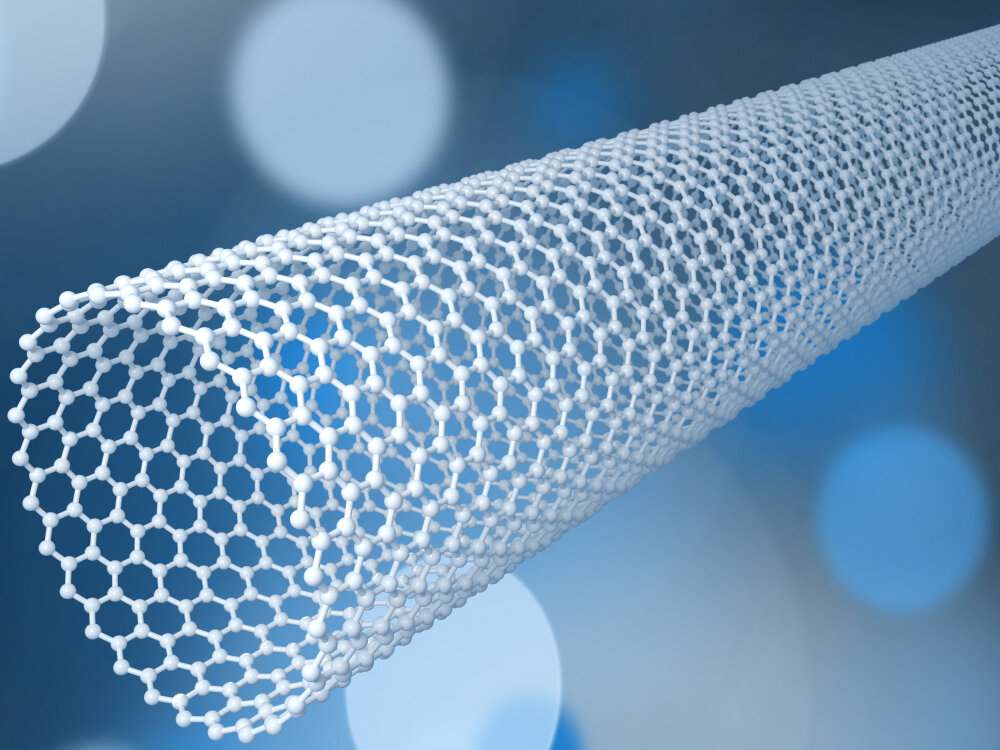
Researchers have developed an insight that could facilitate the production of microscopic carbon nanotubes, structures thousands of times thinner than a human hair used in everything from microchips to sporting goods to pharmaceutical products. The research by scientists at the U.S. Department of Energy's (DOE) Princeton Plasma Physics Laboratory (PPPL) could ensure that fabrication forms nanotubes as efficiently as possible.
The findings are among recent research by scientists working in the PPPL Laboratory for Plasma Nanosynthesis, which pioneers research on low-temperature plasma to improve the production of nanotubes and other nanoparticles. The six-year-old facility has developed a steady flow of insights that could advance that production.
Nanotubes are measured in billionths of a meter, and their flexibility and strength are remarkable. In principle, their tensile strength, or resistance to breaking when stretched, is 100 times greater than that of a same-sized length of steel wire. Scientists are trying to increase their understanding of a widely used technique involving electricity to create plasma, which is then used to create nanotubes.
Engineers use electrical currents known as arcs to vaporize atoms of carbon or other material from a positive component known as an anode. Once in gas form, the released atoms can cohere into nanotubes and other structures that can be used in place of silicon in computer chips to boost performance and energy efficiency. A better understanding could make the production process more reliable and increase the quality of the nanotubes.
PPPL physicists have produced a model showing that nanoparticle formation depends on several factors. The model shows that as the electric current transitions from low-to-high strength, the evaporation, or ablation, rate of the carbon atoms also transitions from low-to-high. This finding is important because researchers want to control ablation at a moderate rather than rapid rate when performing experiments and creating nanoparticles for the industry.
The key factor in the ablation rate is its dependence on background helium gas, which fills the space inside a hollow metal chamber that houses the electrodes. "This is the crucial factor that previous models ignored," said former PPPL physicist Alexander Khrabry, lead author of a paper reporting the findings in the Journal of Applied Physics. "The gas catches the carbon atoms as they ablate and holds them near the surface of the electrode. The atoms then fall back onto the electrode. Under certain conditions, the flux between the gas and the electrodes is high enough to lead to the rapid transition from a low ablation rate to a high one, which is not what we want."
In related research, scientists have developed a novel explanation for the formation of hot spots on one of the electrical components that ablates carbon to help create the nanotubes. Scientists had previously thought that the spots, which form at the positively charged component and interfere with the production of nanotubes, result from instabilities in the current that flows to the negatively charged component like lightning flowing from clouds to the ground.
The new research indicates that the spots form because of the way heat spreads within the anode, meaning that the anode's properties help determine how and when the hot spots form. Hot spots can reduce how many carbon atoms evaporate off the anode's surface and thus reduce how many nanotubes are created. A greater understanding of spot formation could lead to insights into how to reduce or eliminate them.
The process works this way: Heat from the plasma flows within the anode and dissipates at its surface, creating a high-temperature spot. Anode properties that determine the heat flow are therefore important for spot formation and nanotube fabrication. The role of the anode had been overlooked in the past.
A better understanding of such fundamental processes lays the foundation for future advances.
Image: Shutterstock - ustas7777777